Monitorowanie maszyn na przykładzie obrabiarki
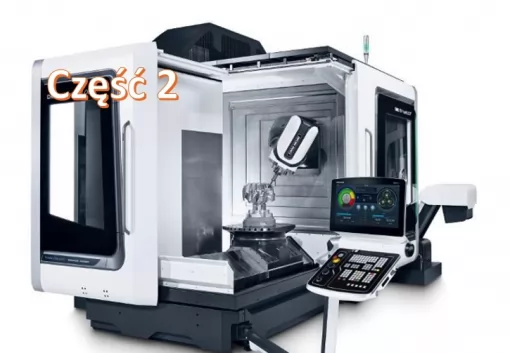
Szeroka wiedza na temat pracy maszyn daje szansę nie tylko na skuteczne zapobieganie ich awariom, ale również pozwala zwiększyć wydajność urządzeń i podnieść jakość wytwarzanych produktów.
Zbieranie bardzo dokładnych danych jest możliwe dzięki zastosowaniu czujników najnowszej generacji. W monitorowaniu pracy maszyn i urządzeń ogromne znaczenie ma pozyskiwanie danych w czasie rzeczywistym. Aby to było możliwe konieczne jest odpowiednie zdefiniowanie obszarów, które są dla zakładu najbardziej istotne i następnie właściwe dobranie czujników.
- "W projektowaniu takich rozwiązań warto posiłkować się specjalistami z różnych dziedzin: wibrodiagnostyki, mechaniki, hydrauliki, elektryki, automatyki, informatyki. Nie trzeba angażować ich na pełen etat do danego zagadnienia. Często wystarczy tylko uzyskać potwierdzenie lub poradę, czy dane rozwiązanie na konkretnej maszynie jest prawidłowe. Najlepiej, gdy w firmie oferującej rozwiązania Przemysłu 4.0 , do każdej grupy produktowej przydzielony jest przynajmniej jeden specjalista. Niestety znam wiele przypadków, że poprzez niewłaściwe zamontowanie czujnika, jego zły dobór albo nieprawidłową parametryzację, otrzymywane dane były bezużyteczne." - mówi Marek Maciejewski z ifm electronic.
Liczy się otoczenie maszyny
Po zamontowaniu czujników, pojawia się kolejne wyzwanie: w jaki sposób analizować przekazywane z nich dane, jak się przekonać, że te parametry są rzeczywiście istotne oraz w jaki sposób należy na nie reagować.
- "Za każdym razem, gdy z klientem planujemy rozpoczęcie monitorowania, bierzemy pod uwagę nie tylko to, czy warto to robić w danym przypadku, ale również zwracamy uwagę na sposób budowy maszyny i jej otoczenie. Inaczej należy podejść do maszyny pracującej na normalnej hali produkcyjnej, a w jeszcze inny sposób do urządzenia w strefie aseptycznej czy w chłodni. W przypadku stosowania wibrodiagnostyki trzeba również wziąć pod uwagę pracę sąsiednich maszyn lub przejeżdżających obok pojazdów, które mogą generować drgania, jak choćby wózki widłowe." – tłumaczy Marek Maciejewski.
Choć można posiłkować się doświadczeniami z podobnej lub takiej samej aplikacji, która została zastosowana w podobnej sytuacji, nie można mieć całkowitej pewności, że dane rozwiązanie zadziała tak samo w innym otoczeniu.
- "Przykładem może być tu monitorowanie przepływu czynnika chłodzącego za pomocą mechatronicznych przepływomierzy z IO-Link, które zastąpiły kryzy, czyli optyczną metodę sprawdzania przepływu, co zastosowaliśmy w jednym z zakładów. Powodem zmiany było to, że kryzy czasem się blokowały. Przepływ spadał głównie z powodu blokowania się kanałów chłodniczych na maszynie. Tymczasem jeśli nie zostanie to w porę zauważone, to maszyna zaczyna produkować odpad i może trwać to nawet całą zmianę. W tym przypadku pojawiły się też wątpliwości, czy dane czujniki przepływu się sprawdzą, ale istniały pozytywne przesłanki do tego, że właśnie tak się stanie. Minęło już pół roku jak pracują bez zarzutu. Takich przykładów mamy całkiem sporo. Wspomniany przepływ to tylko jeden z wielu istotnych parametrów maszyny." – mówi Marek Maciejewski.
Ważne źródła danych
Obrabiarka może się składać z kilkunastu różnych podzespołów, które są ze sobą powiązane. Ich stan będzie wpływał na funkcjonowanie maszyny oraz na jakość, szybkość i efektywność produkowanych elementów. Poprzez odpowiedni dobór czujników można mieć informacje na temat jej funkcjonowania w postaci cyfrowej. Dane mogą pochodzić również z innych urządzeń jak np. sterowniki PLC, regulatory czy urządzenia mierzące pobór energii elektrycznej. Każdy z nich jest wyposażony w inny protokół komunikacyjny, co może powodować dodatkowe implikacje. Dobrym źródłem danych jest także sterownik maszyny.
- "W przypadku projektowania systemu do zbierania danych, dobrze jest określić bazowe wymagania, jak np. zdolność do komunikacji z różnymi systemami. Przykładem może być zdolność odczytu danych z różnych źródeł jak sterowniki PLC Siemens, Beckhoff, Schneider, czujniki, odczyt danych z modułów drganiowych czy pomiaru energii elektrycznej. Istotna jest również skalowalność, czyli otwarta struktura zapewniająca łatwe dopinanie kolejnych elementów. Sprawdza się to, gdy np. dzisiaj potrzebujemy monitorować wrzeciono, jutro zużycie powietrza, a pojutrze energię elektryczną." – tłumaczy Marek Maciejewski.
![]() |
Potrzebne efektywne zbieranie danych
Jeśli na początku wybrana zostanie diagnostyka wrzeciona za pomocą wibrodiagnostyki, to w zależności od tego co będzie monitorowane, można mieć cztery istotne obiekty lub więcej np. vRMS, aRMS, aPeak, ogólny poziom drgań. Po czasie dojdzie również potrzeba monitorowania ciśnienia na chytaku, do tego temperatura silnika i łożyska pompy oraz poziomu, ciśnienia, temperatury i przepływu oleju. Szybko może okazać się, że jedna maszyna generuje kilkadziesiąt parametrów, z których każdy jest istotny.
![]() |
- "Firmy mają bardzo wiele systemów już zainstalowanych, czy to na samych maszynach czy w sterowni, stąd też pojawia się pytanie - po co kolejny? Wszystko zależy od zdefiniowanych wcześniej celów. Jeśli dodatkowy czujnik sprawdzi się w istniejącym systemie, warto się tym zająć. Natomiast jest jedna bardzo istotna zmiana, która powoli materializuje się na naszych oczach. Przedsiębiorstwa dostrzegają potrzebę posiadania systemu, który jest w stanie zapewnić aktualne informacje o tym, w jakim stanie są maszyny oraz które z nich powinny być serwisowane w pierwszej kolejności. Jednak nie chodzi tutaj o kolejną tabelkę w excel-u, tylko o prostą i czytelną informację dostarczoną w odpowiedniej właściwej osobie." – twierdzi Marek Maciejewski.
Klasyczna metoda pozyskiwania danych polega na podpięciu sygnałów do sterownika obrabiarki i "przepuszczenia" ich dalej poprzez sieć ethernet. Wada tego rozwiązania polega na tym, że potrzebne jest przeprogramowanie sterownika, czyli trzeba mieć aktualny program i specjalistę, który jest w stanie to zrobić to profesjonalnie. Ważna jest też mała elastyczność w przypadku rekonfiguracji systemu.
- "Z reguły staramy się unikać takiego rozwiązania gdyż priorytetem jest zachowanie funkcjonowania maszyny. Tymczasem wszelkie modyfikacje w sterowaniu zawsze obarczone są ryzykiem." – tłumaczy Marek Maciejewski.
Topologia Y
Firma ifm electronic zaproponowała rozwiązanie bazujące na topologii Y. Polega ono na tym, że główny strumień danych pochodzących z czujników trafia do systemów IT, a informacje ważne pod kątem sterowania do sterownika PLC.
- "Istotną zaletą tego rozwiązania jest to, że sterownik korzysta z danych potrzebnych tylko do sterowania, a system nadrzędny zbiera wyłącznie te dane, które go interesują w danej chwili. Mamy więc dostęp do wszystkich możliwych informacji w czujniku, ale korzystamy z tych, które są dla nas istotne. Przy realizowanych przez nas projektach zawsze idziemy na pewien kompromis. Jedne dane bierzemy ze sterownika PLC, a inne z dodatkowych czujników lub systemów. Celem projektu jest rozwiązanie konkretnego problemu np. monitorowanie zużycia powietrza, łożysk czy oleju, prowadzące do poprawy ogólnego stanu maszyny. Właśnie na tej podstawie buduje się strukturę systemu dla konkretnego urządzenia." – mówi Marek Maciejewski.
Ważna obserwacja
Choć wdrożenie monitoringu powinno nastąpić szybko, a jego efekty najlepiej, aby były natychmiastowe, to prawie w każdej fabryce specjaliści mają do czynienia z maszynami innego typu. Czasem są one przeniesione z innej fabryki, a nawet z innego kraju. Również sposób komunikacji między nimi jest za każdym razem inny. Niestety taka sytuacja bardzo komplikuje sposób działania. Pomocny może być tu LR Smartobserver, do którego są przesyłane dane w celu wizualizacji, a następnie opcjonalnie do systemów klasy ERP.
Pomimo różnorodności rozwiązań spotykanych w fabrykach możliwe jest wyprowadzenie pewnego rodzaju standardu w pozyskiwaniu danych. Realizacja następuje poprzez zrobienie tzw. projektu pilotażowego, którego celem jest potwierdzenie wcześniej przyjętego założenia. Przykładem jest tu możliwość monitorowania stanu wrzeciona na obrabiarce i reagowanie z wyprzedzeniem na potencjalnie pojawiające się ryzyko awarii.
- "W przypadku, gdy system zgłasza problem lub dokonana jest naprawa, a części zdjęte z maszyny wykazują ślady znacznego zużycia, nie ma przeszkód, aby to rozwiązanie skopiować na pozostałe maszyny tego samego typu. Tak też realizowana jest idea skalowalności. Zaczynamy od jednej maszyny, po czym mając już to doświadczenie, możemy rozszerzyć dane rozwiązanie na pozostałe." – uważa Marek Maciejewski.
Po analizie danych można określić w jakim punkcie się znajdujemy. Poziomy alarmów i ostrzeżeń są ustawiane przez specjalistę w zakresie drgań wg norm lub własnych doświadczeń. Z reguły po ok. 2-3 tygodniach następuje ich weryfikacja i dopasowanie progów dla konkretnej maszyny.
Na podstawie przejrzystych informacji wyświetlanych na ekranie, można obserwować stan maszyn. Jednak samo zbieranie danych nie przejawia większej wartości, jeśli pozostają one zamknięte.
- "Główny cel jest taki, aby informacja była jasna i czytelna, a źródło problemów łatwe do określenia. Użytkownik może sam zmodyfikować widok ekranu dodając interesujące go zdjęcia lub wyświetlając odpowiednie parametry. Jeśli dane, które otrzyma z czujników są dla niego jasne i przejrzyste, można zrealizować kolejny krok - automatycznie powiadamiać o alarmach poprzez SMS lub email. Ponadto jest możliwość wprowadzania zadań technicznych do LR Smartobserver (Maintenance Tasks) celem przekazania ich osobie odpowiedzialnej za dany rejon lub realizację prac w późniejszym terminie." – twierdzi Marek Maciejewski.
Standaryzacja ułatwia życie
Przy bardziej rozbudowanych parkach maszynowych prędzej czy później potrzebne będzie wprowadzenie standardu informującego o stanie maszyn pod kątem predykcyjnego utrzymania ruchu. Każda maszyna ma swój własny interfejs komunikacyjny na linii człowiek-maszyna, czyli lokalny panel operatorski. To dosyć komplikuje sytuację. Ujednolicenie sposobu przekazywania informacji w istotny sposób wpływa bowiem na zarządzanie parkiem maszynowym. Przykładem może być obchód maszyn w celu sprawdzenia ich gotowości do pracy przed rozpoczęciem produkcji.
Systemy klasy ERP (Enterprise Resource Planning) zarządzają kompleksowo przedsiębiorstwem. LR Smartobserver ma na celu zebranie informacji z maszyn, a następnie przedstawić je w sposób łatwy i czytelny. Pozwala również na integrację np. z SAP ERP poprzez Plant Connectivity lub poprzez wysyłanie zgłoszeń o alarmach lub pracach serwisowych.
- "Jeśli chcemy, aby zlecenia na naprawę maszyn i zamówienia części były generowane automatycznie, to musimy mieć pewność, że sygnały, które są wysyłane do ERP są prawidłowe. Ma to związek z poprawnym oczujnikowaniem maszyny, odpowiednim przesyłem danych i ustawieniem wartości brzegowych. LR Smartobserver z ifm zapewnia taką funkcjonalność. Podczas integracji z SAP warto upewnić się, że system przekazuje prawidłowe informacje. W przeciwnym wypadku SAP zamówi nam części, których nie potrzebujemy." – tłumaczy Marek Maciejewski.
Nawet jeśli czujniki zostaną poprawnie dobrane, skonfigurowane i podłączone, to może pojawić się kolejny problemem - jak te informacje efektywnie wykorzystać. Platforma LR Smartobserver daje możliwości zrozumienia w jaki sposób maszyna "przemawia" do człowieka.
- "Powstaje coraz więcej projektów związanych z uczeniem maszynowym, gdzie potrzebne są duże ilości danych. Jednak dane te muszą określać pewne właściwości. Zanim zdecydujemy się uruchomić algorytmy, musimy znać cel tego działania np. algorytm może informować kiedy należy wymienić filtr. Wówczas przedsięwzięcie takie będzie naprawdę użyteczne." – mówi Marek Maciejewski.
Case study, na podstawie którego powstał artykuł, dostępne pod linkiem ->
Przemysł 4.0: Monitorowanie maszyn na przykładzie obrabiarki
Źródło: ifm
- Raport Tokarki CNC i Centra tokarskie - przegląd rynku 2020
- Raport prasy krawędziowe - przegląd rynku 2020
- Kalendarium - przegląd targów przemysłowych 2024
- Branża formierska na Targach INNOFORM®
- ITM Industry Europe - potrójna siła przemysłu
- Żuraw obrotowy w ofercie Weni Solution
- Maszyny używane: Nowe drogi w produkcji przewodów rurowych
- Giętarka trójrolkowa, beztrzpieniowa czy trzpieniowa?
- Czy spawanie laserowe wyprze metody typu TIG i MIG?
- Oerlikon prezentuje innowacje w wirtualnej rzeczywistości VR
- Nowe centrum tokarskie Yamazaki Mazak z 3 głowicami
- Zwinne zarządzanie produkcją jednostkową
- P-Weld – Innowacyjne Rozwiązania w Spawaniu
- Precyzyjna obróbka aluminium – jak wybrać odpowiednią firmę?
- Do kiedy i dla kogo ulga na robotyzację?
- Automatyzacja i systemy magazynowe do blach i dłużyc
- Strategia Produktywności 2030
- Rewolucja w obróbce dzięki wycinarkom laserowym 3D
- Zapisz się na CT | SCAN FORUM Forum Technik CT i Skanowania 3D
- Odbierz zaproszenie na HANNOVER MESSE 2025
- 4 trendy kształtujące przyszłość systemów ERP w 2025 roku
- Raport: Przegląd Rynku Wycinarek Laserowych 2025





