Zoptymalizowana produkcja uwalnia przestrzeń

Przestrzeń w branży wyposażenia laboratoriów uwalniana przez zoptymalizowaną produkcję.
Jednym wiodących producentów sprzętu laboratoryjnego w Europie jest firma Wesemann, która wytwarza zaawansowane systemy ochrony stanowisk pracy oraz najwyższej klasy sprzęt dla laboratoriów i roboczych przestrzeni naukowych, zatrudniając przy tym ponad 200 pracowników. Klienci firmy to podmioty, zajmujące się badaniami i biotechnologią. W celu kontroli prowadzonych procesów biznesowych Wesemann stosuje system proALPHA ERP. Aby zapewnić odpowiednią ilość materiału w danym czasie, w połączeniu z pracownikami i odpowiednimi narzędziami, firma bazuje na proALPHA Advanced Planning and Scheduling. Pozwoliło to firmie Wesemann na znaczną redukcję zapasów.
Wesemann posiada laboratoria rozlokowane po całym świecie – na Antarktydzie, w krajach arabskich, Europie oraz Azji. Zastosowanie komponentów modułowych umożliwia firmie nieograniczone możliwości projektowe i dostosowywanie poszczególnych projektów do indywidualnych preferencji i potrzeb klientów. Wesemann zaopatruje nawet największe, mające po kilka tysięcy metrów kwadratowych laboratoria, dostosowane do danego obszaru geograficznego w wysokiej klasy sprzęt. Projekty tego rodzaju potrzebują wdrożenia procesów produkcyjnych, które są zoptymalizowane, docelowo przekładających się na zmniejszenie zapasów magazynowych i redukcję kosztów. Firma średnio ma około 6 tygodni na wyprodukowanie elementów i zaopatrzenie po zakończeniu etapu planowania produkcji.
Liczy się szybkość
proALPHA APS to serce systemu kontroli produkcji i planowania w firmie Wesemann, będące jednocześnie potężnym narzędziem niezbędnym do optymalizowania niemal każdego procesu produkcyjnego. Zamówienia dzieli się na grupy zanim zostaną dostarczone na miejsce budowy, na podstawie planów projektowych, według pomieszczeń, funkcji produktów czy liczby pięter. Wszystkie grupy posiadają własną datę produkcji, a zlecenia robocze posiadają dodatkowe informacje na temat elementów składowych, które należą do konkretnej grupy, a także materiałach i narzędziach niezbędnych podczas produkcji, osobach, które są za nie odpowiedzialne oraz oczekiwanych zadaniach. Wykorzystanie systemu pozwala również na automatyczne harmonogramowanie zleceń i ich planowanie pod względem zdefiniowanych wcześniej grup. Pozwala to firmie Wesemann na produkcję najważniejszych części z punktu widzenia wstępnego etapu budowy i przechodzenie do kolejnych partii zlecenia. Monitorowanie w czasie rzeczywistym przepływu materiałów pozwala na określenie ich wykorzystania i wydajności. System proALPHA APS proponuje alternatywne zasoby, priorytetyzuje zlecenia produkcyjne i ostrzega o malejących lub przeciążonych zasobach. Dzięki systemowi wielopoziomowego planowania zasobów dostarczane są informacje o wymaganych materiałach, synchronizowana jest dostępność zasobów a pracownicy bezproblemowo mogą radzić sobie z przeciążeniami. Harald Wienberg, szef działu ERP w firmie Wesemann GmbH, tłumaczy: „„Dzięki APS planowanie produkcji w naszym przedsiębiorstwie jest precyzyjne, realistyczne i wydajne”.
Koncepcja precyzyjnego planowania pozwala osiągnąć szczyt
Firma Wesemann, dzięki systemowi proALPHA ma zagwarantowaną możliwość późnego rozpoczęcia produkcji, podobnie jak maksymalnej elastyczności planowania. Jak wyjaśnia Harald Wienberg
- „Nasza codzienna działalność wymaga wielu zmian terminów. Gdybyśmy pracowali według standardowych terminów realizacji, wkrótce zabrakłoby nam miejsca w magazynach”. Zlecenia opóźniają się, gdy na etapie budowy często zmienia się harmonogram. W przypadkach Wesemann w takiej sytuacji gotowa partia nie mogłaby zostać wysłana do klienta i musiałaby być przechowywana w zakładzie, a co za tym idzie, odłożone zostałyby inne, pilne realizacje. Wesemann dąży więc do jak najpóźniejszego rozpoczęcia produkcji roboczych zleceń, by zminimalizować ryzyko. Nawet jeśli mocy produkcyjnych nie starcza, firma sporządza harmonogramy zamówień. Harald Wienberg podkreśla: „Pomaga nam to uniknąć problemów w przypadku opóźnień w realizacji zamówień. Narzędzie do planowania terminowego daje nam wgląd we wszystkie zmiany w harmonogramie. Dzięki niemu możemy szybko zmienić porządek prac, aby zapewnić terminową dostawę części na plac budowy”.
Większa przestrzeń – większe możliwości
75% powierzchni magazynowej firmy Wesemann zostało zwolnione i przekształcone w obszary produkcyjne, dzięki proALPHA. Zmniejszenie zapasów i optymalizacja przepływu materiałów możliwe są dzięki szczegółowemu planowaniu.
- „Teraz całkowicie rezygnujemy z zapasów interwencyjnych” – wyjaśnia Harald Wienberg. Wesemann planuje wykorzystywać większość modułów wykonywanych na zamówienie, by mogły być one magazynowane tylko przez tydzień, zanim wykorzysta się je do realizacji zamówienia. Te same części zajmowały wcześniej połowę powierzchni magazynowej i przechowywane były 5 tygodni.
Harald Wienberg tłumaczy:
- „Wolną przestrzeń magazynową wykorzystaliśmy do zainstalowania nowej lakierni proszkowej. Jej wydajność jest o 50% wyższa i pozwala na szybką zmianę kolorów, dzięki czemu możemy dostosować produkcję do wymagań klienta. Tę strategię stosujemy również w innych obszarach produkcji, budując dodatkowe stanowiska pracy, co nie tylko oznacza dla nas wartość dodaną, ale również pomaga nam zwiększyć niezawodność planowania i dostaw”.
Just-in-Time – system produkcji
Do tej pory firma Wesemann koncentrowała się na takim systemie produkcji, który zakłada możliwie jak najwcześniejsze rozpoczęcie procesów. Miało to zapobiec brakom w zakresie szczególnego planowania i stanowić zabezpieczenie. Dzięki systemowi proALPHA APS firma znacznie zwiększyła wydajność produkcji, a kolejny cel Harald Wienberg określa następująco:
- „Chcemy w średniej perspektywie czasowej osiągnąć produkcję just-in-time, stosowaną w przemyśle samochodowym”.
System proALPHA Finite Planning umożliwia realizację tego celu w szybkim czasie. W 2013 roku firma Wesemann zaczęła reorganizować zakład, została opracowana całkowicie nowa strategia produkcji przez firmę doradczą. W 2016 roku Wesemann rozpoczęła się reorganizacja działu obróbki metali. Zainstalowano zupełnie nową lakiernię proszkową, a pozostałe stanowiska pracy zostały zreorganizowane – sekcja do obróbki aluminium wraz z cięciem, roboty i lasery. Firma Wesemann dąży do dostosowania procesów produkcyjnych do wymagań klientów dzięki oferowanym przez proALPHA Finite Planning projektom i szczegółowym rozwiązaniom.
- „Produkcja w modelu Just-in-Time jest dla nas nie tylko realistycznym celem, lecz również idealnym rozwiązaniem, które pozwoli nam sprostać wyzwaniom codziennej działalności”.
Źródło: proALPHA
- Raport Tokarki CNC i Centra tokarskie - przegląd rynku 2020
- Raport prasy krawędziowe - przegląd rynku 2020
- Kalendarium - przegląd targów przemysłowych 2024
- Branża formierska na Targach INNOFORM®
- ITM Industry Europe - potrójna siła przemysłu
- Żuraw obrotowy w ofercie Weni Solution
- Maszyny używane: Nowe drogi w produkcji przewodów rurowych
- Giętarka trójrolkowa, beztrzpieniowa czy trzpieniowa?
- Czy spawanie laserowe wyprze metody typu TIG i MIG?
- Oerlikon prezentuje innowacje w wirtualnej rzeczywistości VR
- Nowe centrum tokarskie Yamazaki Mazak z 3 głowicami
- PIE: Dobre prognozy na 2025 rok
- Zwinne zarządzanie produkcją jednostkową
- Mazak Open House
- Dynamika przemysłu w październiku 2024 roku
- Podstawowe typy łożysk precyzyjnych i ich charakterystyka
- P-Weld – Innowacyjne Rozwiązania w Spawaniu
- Dynamika przemysłu w listopadzie 2024 roku
- Przemysłowa Wiosna 2025 - ruszyła rejestracja
- Precyzyjna obróbka aluminium – jak wybrać odpowiednią firmę?
- Do kiedy i dla kogo ulga na robotyzację?
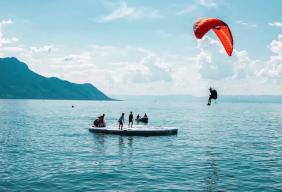
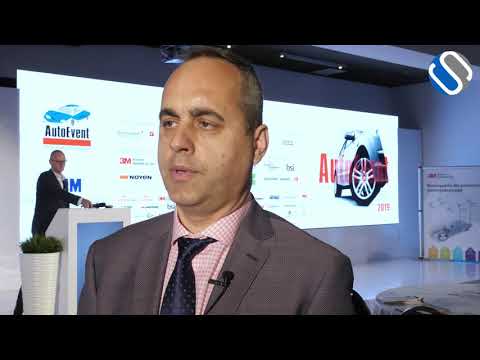
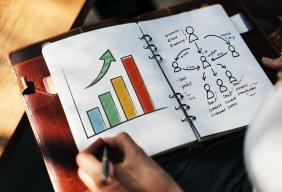
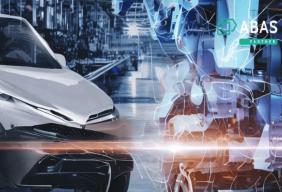
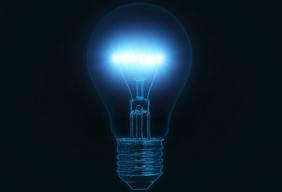
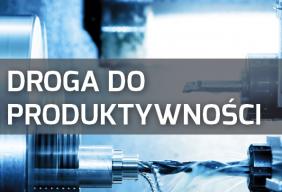